Beläge spielen eine entscheidende Rolle beim Schutz der Trommel Ihrer Förderbandanlage, erhöht die Bandreibung und reduziert abrasiven Verschleiß sowie Materialablagerungen. Es ist die Materialschicht, die mit dem Mantel einer Fördertrommel verbunden ist und typischerweise mit Gummi, Keramik, Polyurethan oder anderen Materialien beschichtet ist. Das gewählte Material hängt stark von Ihrer spezifischen Anwendung ab, wie in unserem Blog über Auswahl der Beläge für Ihren Betrieb erläutert.
Und da Polyurethan-Beläge immer beliebter werden, haben wir uns entschlossen, die Vor- und Nachteile von Polyurethan-Belägen gegenüber Vollkeramik-Belägen zu untersuchen. Lesen Sie weiter die Abwägung der Fakten.
Die Vor- und Nachteile von Polyurethan-Belägen auf Ihrer Förderanlage
Polyurethan, auch als Kunststoffbelag bekannt, hat bei Anwendungen mit nicht angetriebener Trommel an Popularität gewonnen, bei denen Bedenken hinsichtlich der Ansammlung von Rücktrag zwischen Band und Belag bestehen. Es kann als Platte oder Streifen aufgebracht werden, entweder mit gummiertem Polyurethan verbunden oder direkt auf den Trommelmantel gegossen werden. Im Vergleich zu Gummibelägen hat es eine drei- bis fünfmal längere Lebensdauer und bietet eine höhere Abriebfestigkeit. Der niedrige Reibungskoeffizient macht den Polyurethanbelag schonend für die Bandunterseite und ist damit die ideale Lösung für Bänder mit vorzeitigem Verschleiß. Auch die Beschädigungsgefahr der Bandabdeckung ist durch den Polyurethanbelag sehr gering. Er wird häufig bei Umlenktrommeln verwendet, bei denen ein Schlupf zwischen dem Band und der Belagoberfläche auftritt.
Gegossene Polyurethanbeläge sind jedoch sehr teuer in der Anwendung und äußerst schwierig zu reparieren, sie werden im Allgemeinen nur verwendet, wenn sich Gummi- oder Keramikbeläge als weniger brauchbar erwiesen haben. Darüber hinaus hält ein Polyurethanbelag maximal fünf Jahre, bevor die Trommel erneuert werden muss. Wie bereits erwähnt, ist dies ein sehr kostspieliges und arbeitsintensives Verfahren, daher wird empfohlen, Polyurethan nur für Umlenktrommeln und nicht angetriebene Trommeln auf Wendeförderbändern zu verwenden.
Die Vor- und Nachteile von Keramikbelägen auf Ihrer Förderanlage
Keramikbeläge sind bei Anwendungen beliebt, bei denen Bandschlupf oder hoher Verschleiß ein Problem darstellen, da sie haltbarer als Gummi sind. Die gängigsten Arten von Keramikbelägen haben entweder glatte oder genoppte Keramikplatten, die beide eine deutliche Erhöhung der Reibung, der Griffigkeit und der Spurführung des Bandes bieten.
Keramikbeläge haben gegenüber anderen Arten von Belägen vier Hauptvorteile:
1) Die Keramikplatten sind extrem abriebfest, sodass sie härtere Materialien handhaben können. Die Noppen können die Traktion der Antriebstrommeln außerdem erheblich verbessern.
2) Die Menge der Abdeckung auf der Oberfläche des Belags kann an Ihre Anwendung und Ihre Anforderungen angepasst werden, mit Optionen von 13 %, 39 % und 80 % Keramikabdeckung.
3) Keramikbeläge haben eine höhere Lebensdauer, was den Belagverschleiß deutlich reduziert.
4) Ein glatter Keramikbelag ist die optimale Wahl für nicht angetriebene Kopftrommeln; er weist eine flache, ebene Oberfläche auf, damit das Band und die Bandabstreifer effizient betrieben werden.
Bei der Installation von Keramikbelägen gibt es nicht viele Nachteile zu beachten, aber bei der Auswahl des richtigen Belags für Ihr Förderbandsystem ist es am besten, sich fachkundige Hilfe zu holen. Je nach Förderdesign können bei der Auswahl von Noppen-Keramikbelägen beispielsweise Bandzerkratzungen oder Schäden an der unteren Abdeckung auftreten, wenn Bandschlupf vorhanden ist, da die Noppen die Rückseite des Bandes zerkratzen können. Daher ist es sinnvoll, sich bei der Auswahl des für Ihre Anlage am besten geeigneten Belag an einen Experten zu wenden.
Welcher Förderbandbelag ist also der beste?
Polyurethan- und glatte Keramikbeläge sind beide akzeptable Optionen, wenn Sie entscheiden, welcher Belag für Ihre nicht angetriebene Kopftrommel am besten geeignet ist. Wenn Sie jedoch eine kostengünstige Entscheidung treffen möchten, die Ihre Produktivität nachhaltig steigert, ist Vollkeramik die optimale Wahl.
In den meisten Anwendungen hat ein Polyurethan-Belag eine maximale Lebensdauer von fünf Jahren, während ein glatter Keramikbelag bei derselben Anwendung nachweislich mindestens 20 Jahre hält. Nicht nur die anfänglichen Produkt- und Installationskosten sind viel günstiger; Außerdem sparen Sie sich über die Lebensdauer des Belags die Kosten für einen Austausch, der mindestens drei- bis viermal stattfindet.
Im Mai 2001 installierte Flexco einen Flex-Lag®-Vollkeramik-Trommelbelag in Eisenerz. Nach 20 Jahren ist er immer noch in perfektem Zustand, wie im Bild unten zu sehen ist. Lesen Sie hier die vollständige Fallstudie.
Kontaktieren Sie einen Fachmann zur Beratung für Ihren Belag
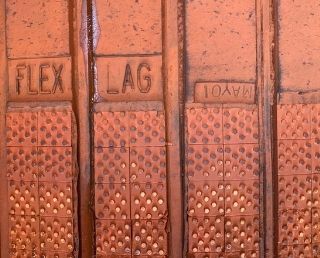 |
Flex-Lag®-Vollkeramik-Trommelbelag, der im Mai 2001 installiert wurde |
Neben Popularität und Preis ist vor allem der Einsatz in Ihrer spezifischen Anwendung für die Auswahl der Art des Trommelbelags ausschlaggebend: zu beachten sind das Förderdesign, der Produktabrieb, der Trommeltyp und die Bandgeschwindigkeit. Es ist für Ihren Betrieb von entscheidender Bedeutung, dass ein Experte diese Faktoren bestimmt und abwägt, welches Material für Ihre Fördertrommel am besten geeignet ist.
Wir bei Flexco glauben fest daran, die besten Lösungen und Technologien für Ihre spezifischen Anwendungen und Betriebsbedingungen zu finden. Melden Sie sich für eine kostenlose Bewertung an, und ein lokaler Außendienstler kommt in Ihren Betrieb und hilft Ihnen, den richtigen Belag für Ihre Förderanlage auszuwählen.
Autor: Phil Dreghorn, Regional Manager
Dreghorn kam 2003 als Sales Manager von Queensland zu Flexco. Vor seiner Tätigkeit bei Flexco hatte Dreghorn verschiedene Positionen in der Branche der Förderanlagen inne, die die Wartung von Förderbändern und das Verbinden von Bändern umfassten, und hat ein besonderes Interesse an Produkten mit Belägen. Dreghorn verfügt über eine Ausbildung zum Kesselschmied und Fachmann für Förderbandverbindungen sowie eine Ausbildung zum Arbeitsschutzbeauftragten.