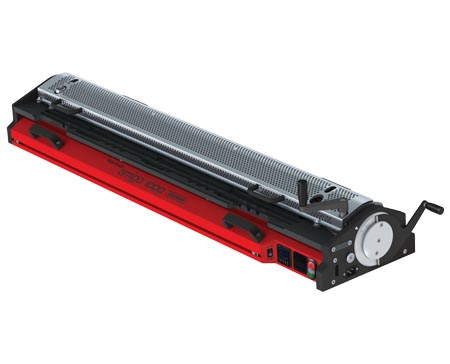
Branche
Bäckerei
Anwendung
Beförderung gebackener Kekse
Produkt
Schweißpresse Novitool® Amigo™
Ziel
Zeitersparnis
Anfertigung konsistenter Verbindungen
Arbeitssicherheit
Angaben zur Förderanlage
Mehrere Ausführungen von monolithischen Förderbändern
Problem:
In einer großen Bäckerei war man weder mit Qualität, noch Stabilität der Verbindungen der dortigen Förderbänder zufrieden.
Zum einen gab es ein Problem mit den Stillstandzeiten. Die Förderbänder mussten miteinander verbunden werden und bedauerlicherweise erforderten die vom Wartungspersonal für die Anfertigung von Stoßverbindungen verwendeten Werkzeuge für die Vollendung der Arbeiten 30 Minuten einschließlich Vorwärmzeit. Das zweite Problem ergab sich aus den Leistungseigenschaften der erstellten Verbindungen. Die Verbindungen, die eingebaut wurden, waren instabil, was zu vorzeitigem Betriebsversagen führte – und dies bisweilen zu äußerst ungünstigen Zeitpunkten. Da Mitarbeiter aus verschiedenen Arbeitsschichten mit unterschiedlicher Arbeitserfahrung die Förderbänder verbinden mussten, waren diese häufig instabil und es kam zu Lufteinschlüssen. Die handwerklichen Fähigkeiten der Mitarbeiter schlugen sich beim Einsatz der herkömmlichen Werkzeuge auf die Verbindungen nieder.
Schließlich erforderten die veralteten Techniken für die Herstellung von Förderband-Verbindungen Montageprozesse, die sich als schwierig, ineffizient und vor allem als gefährlich erwiesen. Der Kunde verwendete je nach Förderbandtyp zwei verschiedene Systeme für die Herstellung von Förderband-Verbindungen. Beim ersten Typ kommt ein Heizstab mit einer Schablonenvorrichtung zur Anwendung. Der Heizstab ist ungeschützt und erreicht extrem gefährliche Temperaturwerte. Daraus ergibt sich sowohl für das Bedienpersonal als auch für im Einzugsbereich befindliche Personen eine unsichere Arbeitsumgebung. Das zweite System wirft ebenfalls Probleme auf. Das Bedienpersonal muss die Förderbandenden mit einem Drehwerkzeug anfassen, um zwischen den beiden Bandenden mit einer ungeschützten Heißluftpistole eine Urethanstange einschweißen zu können.
Lösung:
Nach Teilnahme an einer Vorführung der Schweißpresse Novitool® Amigo™, die speziell für die Verbindung monolithischer Bänder konstruiert wurde, war das Wartungsteam über die Ergebnisse erstaunt und entschloss sich für einen Einsatz im Rahmen bevorstehender Reparaturen. Die Wartungsmannschaft hat das Werkzeug vom Typ Amigo zur Herstellung der Verbindung unmittelbar an das Förderband herangefahren und dabei festgestellt, dass sich in jedem Arbeitsschritt Vorteile ergeben. Der erste Schritt bestand im Zuschneiden der Förderbandenden auf die korrekte Länge. Man begann mit der Auswahl der Schablone für das zu verwendende Band. Am Modell Amigo stehen 10 Schablonen zur Auswahl, welche die Mehrheit aller heute auf dem Markt erhältlichen monolithischen Bänder abdeckt. Der Kunde verfügt tatsächlich über drei verschiedene Arten von Förderbändern innerhalb der verwendeten Einrichtung, sodass sich das Modell Amigo dort als vielseitig einsetzbares Werkzeug zur Herstellung von Förderband-Verbindungen erweist. Nach Auswahl der richtigen Schablone und sicherem Einspannen des Förderbands ermöglicht die integrierte Klinge ein sicheres, schnelles und effizientes Verfahren zum Erstellen eines genauen Schnittprofils.
Der nächste Schritt im Verfahren betraf das Entfernen von Feuchtigkeit von den Bandenden vor einer Herstellung der Verbindung unter Verwendung der Vorwärmfunktion. Beim aktuellen Verfahren würde diese Feuchtigkeit zur Bildung unerwünschter Lufteinschlüsse in der vollendeten Bandverbindung führen, was mit der Amigo Schweißpresse aber nicht auftritt.
Außerdem liegt ein weiterer Vorteil in der eigentlichen Herstellung der Verbindung. Die Wärmequelle zum Schmelzen der Förderbandenden gerät niemals mit diesen in Kontakt und, was wichtiger ist, gerät niemals in Kontakt mit dem Bedienpersonal. Außerdem muss sich die Hitzeabschirmung für eine ordnungsgemäße Funktion in der richtigen Position befinden, sodass das Bedienpersonal während des Verfahrens zur Verbindungsherstellung stets geschützt bleibt. Weil ein Kontakt mit den Bandenden ausgeschlossen ist wird das Material während des Verbindungsvorgangs nicht gestört und so die Anfertigung einer optimalen Förderbandverbindung ermöglicht. Der tatsächliche Zeitaufwand pro Verbindung lag im Durchschnitt bei nur etwas über einer Minute. Ein weiteres Sicherheitsmerkmal wird bei Vollendung der Förderband-Verbindung erkennbar. Nach Abschluss der Arbeiten wird das Heizelement gleichzeitig in die Einlagerungsposition bewegt, sodass für das Bedienpersonal keinerlei Möglichkeit von Verbrennungen besteht.
Ergebnis:
Das erste verbundene Förderband benötigte für das Vorwärmen nur 300 Sekunden und für die Verbindungsherstellung nur 55 Sekunden, bei einem Zeitaufwand von insgesamt nur 6 Minuten. Die Einstellungen für das zweite Band betrugen jeweils 600 Sekunden Vorwärmzeit, gefolgt von 80 Sekunden Verweildauer für die Herstellung der Verbindung. Beide Verbindungen waren wesentlich weniger zeitaufwändig, als es bei Anwendung der vorhandenen Werkzeuge der Fall ist. Die Bäckerei verfügt nun über ein einzelnes Werkzeug zur Herstellung von Verbindungen an allen unterschiedlichen Ausführungen monolithischer Bänder und dies schnell, genau und sicher.