Raise your hand if you have a belt cleaner installed on your conveyor system but haven’t checked the tension recently. We’ve all been there. With the limited amount of time you have on a shutdown to install, maintain, or refurbish your belt cleaners, getting the tensioning right can sometimes be overlooked.
Why is belt cleaner tensioning important? Because without correct tensioning, belt cleaner performance is seriously compromised, which directly affects the efficiency of the conveyor system. Maintaining optimal tension on belt cleaner blades provides more efficient cleaning while protecting the belt and reducing carryback. Proper tensioning leads to a thorough cleaning, which increases system productivity and safety. Correct tension also ensures you are getting the maximum amount of life from your polyurethane or metal blades.
Over-Tensioning – Does It Cause Problems?
You would be forgiven for thinking that over-tensioning your belt cleaner is okay. The more pressure the cleaner blades have on the belt, the better the clean, right? However, this is a common misconception. In fact, over-tensioning does not improve the performance of the belt cleaner. It is actually more likely to reduce belt cleaner efficiency, reduce blade life, and can cause serious problems for your belt conveyor system.
Excessive friction and vibration from over-tensioning with urethane blades can create internal temperatures up to 120˚C (250˚F). Hysteresis and thermal changes can cause overheating in portions of the blade, which can result in blisters and melting. Once this occurs, the blade is mostly useless against battling carryback, and could even cause damage to your belt.
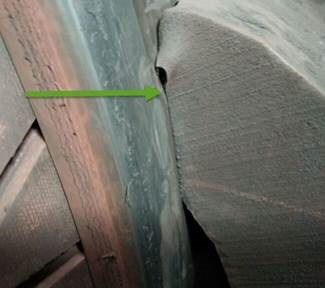
Pictured: Melted urethane blades that have overheated
due to excessive friction and vibration caused by over-tensioning.
Under-Tensioning – Yes, This Can Cause Problems Too
Similar instances occur when tensioning is too aggressive on metal blades – they experience an excessive rise in temperature. This heat easily transfers to the belt, which is typically the most expensive component of the belt conveyor system. Then, when the belt stops, the metal blade can actually “melt” the belt, burning through the top layer of belt material. This could lead to expensive belt repairs and unplanned downtime.
Another common misconception is that if the belt cleaner lacks proper tensioning, then it is harmless to your belt conveyor system. In reality, under-tensioning your belt cleaner, or having inconsistent maintenance processes, can be just as problematic for maintenance teams as over-tensioning.
Without enough tension on the belt cleaner blades, metal or polyurethane blades can bounce or chatter leading to shorter blade life, and an increase in carryback on the conveyor system. For metal blades, chatter can also cause significant damage to the belt, leaving marks across its width. If not addressed, this can also create a snowball effect where the chatter marks will get worse over time because the marks themselves cause additional chatter.
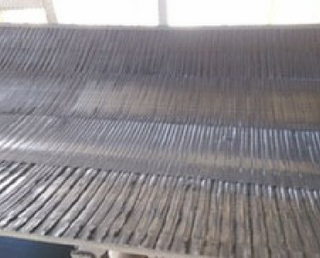
Pictured: Chattering or bouncing metal blades can cause
significant damage to the belt, leaving marks across its width
and making it much more difficult to clean.
If your belt cleaner isn’t cleaning effectively, then it’s likely to cause excessive carryback. Carryback is wasted product that is time-consuming to clean up and can cause belt mistracking, which leads to problems with spillage and damage to the edge of your belt.
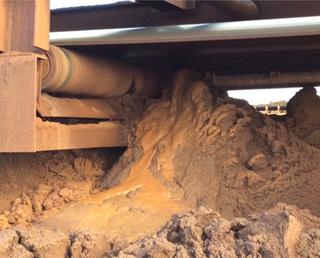
Pictured: Excessive carryback due to ineffective belt cleaning.
Ineffective cleaning can also cause the material to build up on the surface of the belt, making the belt abrasive and increasing blade wear. Material buildup causes the top cover of the belt to wear too, and worn top covers are harder to keep clean. It’s all sounding time-consuming and expensive, isn’t it?
Optimal Belt Cleaner Tensioning – Maintenance Is Key
All these factors increase the need for maintenance and repairs, as well as added labour cost to clean up around the conveyor. So what does optimal tensioning look like?
At optimal tensioning, belt cleaning is at its most efficient. Blade life is maximised, and wear to other belt conveyor components is minimised. So how do you achieve optimal belt cleaner tension?
All cleaners require maintenance, especially tensioning. Regular observation and tension checks allow you to make the adjustments needed to keep your belt clean, productive, and safe. Choosing a tensioner that makes checking and adjusting the cleaner convenient and easy helps ensure optimal cleaning.
Luckily, there are some good options available to make checking belt cleaner tensioning as simple and quick as possible for time-poor maintenance teams. The first option is to select a system with a simple, intuitive, and easy-to-access visual tension check. Making this process simple will lead to more frequent checks and overall better performance.
Another option is to utilise an air tensioning system that will maintain constant pressure throughout the life of each blade. This is by no means a set and forget – you’ll still want to monitor the pressure gauge! However, with simple adjustments at the regulator, you can ensure the cleaner is at its optimal tension for peak performance throughout the full blade life.
Today more than ever, maintenance managers are trying to make their belt conveyor systems as efficient as possible. Getting the correct tension on your belt cleaners is a fast and simple change you can make that will have a big impact on the productivity of your system.
If you are considering if you need a belt cleaner on your system, check out this blog post I wrote that illustrates the importance of a properly installed, professional conveyor belt cleaner.
Authored By: Kevin Fales, Product Manager
Fales manages the belt conveyor product (BCP) line, providing product development and engineering with guidance on market requirements for both new product concepts and existing products. He also leads the development of technical and promotional literature supporting BCP line. Fales graduated from Grand Valley State University with a bachelor’s degree in Marketing and is currently working toward his master’s degree in business administration from Western Michigan University.