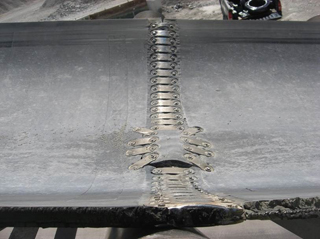 |
Splice repaired with belt patch and Flexco® Bolt Solid Plate Fasteners. |
One of your belt rollers has failed, cracked open, and became a giant pizza cutter, creating a massive rip in your belt. Your operation is at a standstill and you either don’t have the budget to bring in a service crew to make the fix, or they aren’t scheduling visits right now because they are short staffed with all that’s going on in the world today. But you’re on a deadline and you can’t afford a break in the action.
Time to fix your belt with rip repair fasteners.
Before you get started …
While rip repair fasteners are quick and easy to use, we’d recommend taking a peek at this Rip Repair video. In it, Training and Technical Specialist Russ Heintz, walks you through performing a conveyor belt rip repair with Flexco® Bolt Solid Plate Fasteners. Russ also just wrote a blog on Rip Repair Best Practices that you might want to review ahead of the repair.
Now to the tips …
We really do get a lot of questions about rip repair, and we’ve also gotten a lot of feedback from operators across the globe on how to maximize your efforts and cut time while installing the fasteners. So I reached out to our field technicians, training specialists, and territory managers and put together a list of rip repair “do’s and don’ts.”
First, the “Do’s”:
DO know that you can install rip repair fasteners from either the topside or bottom side of the belt, depending on where your rip is. Unlike regular splice installation, rip repair doesn’t utilize a templet and you are only installing one fastener at a time so there is no need to drag all your tools to the topside of the belt to get the job done.
DO use the fastener as a templet to mark holes. Punch holes biased on the outer edge to ensure the belt is drawn tight when the plates are secured.
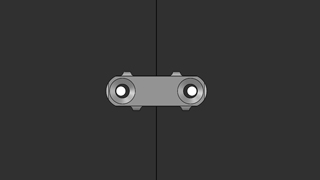 |
When punching holes, use the fastener as a template, exaggerating the dimensions slightly. |
DO install fasteners starting from one end and working towards opposite end. With traditional splicing, we recommend beginning at the ends and working your way towards the middle. For rip repair, you install fasteners in order from one end to the other.
DO apply fasteners on the corners first, and then on the sides when applying patches. This will secure the patch so you can continue with the rip repair.
DO space your fasteners in accordance with the material you are conveying. Spacing should allow no material to seep through. For finer materials like sand, space the fasteners closer to each other. If using a Turtle #16 fastener, space each fastener from four to six inches apart for best results until you can get a more permanent solution.
DO install three-bolt rip repair fasteners perpendicularly to the edge of the belt for smooth travel over pulleys.
DO use the proper tools when installing rip repair fasteners to maintain the integrity of the belt carcass, including portable hand or power tools, a punch or boring bit, a wrench, and bolt breakers.
DO grind bolt end flush with the belt. Pro tip: You can use a grinder to speed up the process of breaking off the bolts. You can also use a grinding wheel to replace a plate by simply creating a small groove in the nut to match the cracking chisel in order to remove it quickly and easily. Just make sure you don’t damage the belt with the grinder.
Next, the “Don’ts”:
DON’T install three-bolt rip repair fasteners lengthwise on the belt. For smoother running over pulleys, three-bolt rip repair fasteners are always applied crosswise on the belt.
DON’T use three-bolt fasteners when the repair is in the troughing junction. They are too large and will not bend, putting stress on the belt when it’s troughing and causing more damage.
DON’T use rip repair fasteners for transverse repairs over 25% of the belt width. If you have a belt that sustained this much damage, cut out the damaged belt and install a new mechanical belt fastener splice.
DON’T use three-bolt rip repair or Turtle fasteners to join belt ends together as a complete splice. The Turtle fastener is not rated for this and the three-bolt fasteners should never be travelling lengthwise over the pulley.
One final note
My last, and most important, tip is to make sure you are using the proper fasteners for your rip repair. For quick and easy rip repairs, we recommend Flexco Repair Fasteners, with available belt thicknesses ranging from ¼ to 1 ¼” thick (6mm to 32mm). When used with extra-long bolts, maximum belt thickness is 2” (50mm). They offer unmatched plate compression and piloted bolts for quick and easy installation. Flexco even offers Rip Repair Kits, which contain all the tools and fasteners you need to fix your belt and be back up and running in no time.
Authored by Aaron Rosso, Senior Product Manager
Rosso is responsible for managing the heavy-duty mechanical belt fastener program globally for Flexco, including the program vision and strategy, product development plan, product line portfolio, promotion, PR and communications, pricing, and profitability. Rosso graduated from Western Michigan University with a bachelor’s degree in Finance and received his master’s degree in business administration from the Kellogg School of Management at Northwestern University with a concentration in Marketing and Strategy.