Modes of Roller Failure
Rollers fail in many different ways. Learning the modes of failure will help you when deciding what rollers are best for your conveyor belt system. There are many different causes of roller failure, but the most common are abrasion and corrosion, seal failure and end disk failure.
Abrasion and Corrosion
Regular surface wear or abrasion from belt contact can limit the roller life dramatically. On site, this may be known as ”general wear and tear.” However, it’s important to know that by specifying a roller designed to withstand the conditions of your site, the longevity of the product will increase.
For example, if your roller is prematurely wearing due to corrosion, it’s natural that the rate of abrasion will accelerate and the steel surface will weaken quickly. However, by choosing a polymer roller (like engineered nylon and HDPE) over steel, the rate of will decrease significantly and you’ll gain more life from your roller. The best part? You’ll also be saving money on replacement rollers and the cost of maintenance.
Seal Design
Seal design is key to the success of the bearing and roller. A seal design that is resistant to moisture and other fines protects the roller from contamination and internal corrosion. It is estimated that 43 per cent of bearing failures come from moisture and other contaminants.
To prevent this type of failure, choose a roller with a quality centrifugal flinger seal. This feature offers up to nine times more centrifugal force, to help “spin out” fines, water, and other contaminants. The design of the flinger seal discourages the entry of contaminants and protects the bearing inside the roller.
End Disk Failure
End disks can be made of durable materials, but the method used to join the end disk to the core can make an impact on the life of your roller. Every roller has a core and roller end pieces, and if they come apart, the result can be disastrous for your belt. With steel rollers, the end disk separating from the core can act like a sharp knife, cutting your belt.
This is purely a quality issue, so it’s important that you research your suppliers’ manufacturing methods, research and development processes, and ongoing support plans. This will ensure that the roller you invest in won’t cost you thousands of dollars in belt repair.
Roller Failure in Real-Life
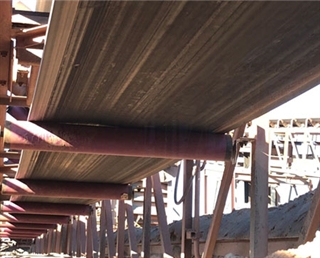 |
CoreTech™ Rollers at the Iron Ore Site |
An Australian iron ore mine was constantly struggling with their steel rollers. The main issue was the short wear life of the product. As the roller casing was quickly wearing out, the bearings were also prematurely failing – mainly due to rapid wear of the bearing seal. This resulted in a “pizza cutter” effect, where the seized rollers would cause severe damage to the bottom cover of the conveyor belt.
The secondary issue was that the ore product was constantly sticking to the roller shell. The build-up of product was causing severe tracking issues and contributing to further wear of the belt.
After assessing the challenges faced by the mine, Flexco and a local Flexco distributor, encouraged the maintenance team to try Flexco CoreTech™ Rollers. The rollers are made from extruded nylon, so material easily sheds off the roller instead of creating a build-up. The rollers also feature a centrifugal seal with static ends, meaning even if the roller did fail, the bearing would not cut through the belt. The site agreed to a trial period on one conveyor.
Over each shutdown, the CoreTech rollers were monitored for wear and failures, with photos taken as a record. The site was so impressed with the results on the trial conveyor that they proceeded to switch out the steel rollers on another two conveyors with the CoreTech rollers as well. None of the rollers failed due to wear, and a full-site roller change-out is scheduled in the future.
Authored by: Jayden Baker, WA/SA Territory Manager
Baker began working at Flexco in 2014 as a Territory Manager in Western Australia, before taking the same management role for South Australia in addition to his current duties. He has worked in mining for 15 years, specialising in machine and automation safety. Baker holds qualifications in management, boiler making, and mechanical fitting.