You’re about to install a splice in your belt. You’ve chosen the correct fastener and strip length. You chose the material for the fastener based on your application, and you even know how you’re going to go about installing it. What is missing in this equation? The hinge pin. While a lot of attention is paid to the fastener and its strength and durability, it’s really the hinge pin that can, quite literally, make or break your splice. Hinge pins simply don’t get enough attention.
Why is a hinge pin important?
The hinge pin is critical to the integrity of the splice. It is a vital link that, when combined with properly selected and installed hooks, complete the perfect belt splice system. A properly specified splice (hook and pin) delivers long life performance and minimizes unscheduled downtime. Unfortunately, the selection of a hinge pin is often an afterthought and can make inserting and removing the pin troublesome. This is particularly important if your operation requires frequent belt cleaning and if removing the belt is necessary.
It all starts with selecting the proper hinge pin. Many users substitute various materials such as welding rod, baling wire, etc. instead of matching the correct pin to the application. While this may seem harmless at the time, incorrect material usage or undersized/oversized pin diameter may result in pin breakage, premature wear of fastener loops, and unscheduled downtime.
Click here to learn more about the characteristics of different hinge pins (also referred to as connecting pins).
Selecting the proper pin
So first and foremost, put a little time into choosing the correct pin. You can start by talking to field experts or your belt hook and pin distributor. They have broad experience that can help you guide your decision and avoid potential problems down the road. When choosing the correct hinge pin for your application, there are many different facets to consider, including: pin wear, hook wear, rigidity, magnetism, flexibility, and composition of the pin. Above all, choose a hinge pin that is designed to provide long pin life and minimal wear to fastener loops, keeping your application in mind.
Inserting your hinge pin
Inserting hinge pins into a wide belt can be difficult and time-consuming, especially with a flexible hinge pin. This operation can become complicated if you are doing a field installation on top of the conveyor belt structure. Using a pin with a leader can minimize the effort of inserting the pin into the splice. A “leader” is a rigid, smaller-diameter pin that is attached to the hinge pin to help guide the larger diameter hinge pin through the splice. Depending on the hinge pin that has been chosen, the leader is formed in one of two methods:
Swaged Leader assemblies use a Nylon Plus pin or one of the flexible cables – Nylon Covered Stainless Cable, Bare Stainless Cable, or DuraLink™. In this process, a small diameter music wire is swaged onto the hinge pin, forming a leader.
- With a Stripped Leader, a portion of the nylon coating of the Nylosteel, Nylostainless, or DuraStainless™ pins can be stripped off, exposing the solid core. This stripped portion forms a leader. Both leaders can be fed through the width of the splice, allowing the hinge pin to be pulled through with ease. The leader is then cut off and discarded.
Removing your hinge pin
To lock your pin into the splice, simply strip ½” (12 mm) of the nylon coating and form a “J” on the end of the pin. This process secures the pin, preventing it from migrating out of the splice. In addition, the “J” end does not allow the pin to spin freely within the splice and focuses the wear on only one side of the pin.
To remove, you can simply pull the pin until the “J” end is out of the splice, rotate the pin 90-degrees until the smooth side of the pin is against the fastener loops, and then pull the pin out.
Replacing your hinge pin
It is also important to know when to replace the pin. Inspection of hinge pins and replacement when necessary is critical to achieving a long splice life. When grooves worn by the fastener loops exceed 25 percent of the pin diameter, the pin should be replaced. Excessive pin wear can also cause unwanted wear in the loop area of the fasteners, so those should also be inspected closely.
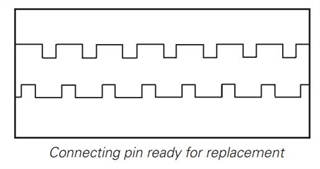
In addition, the pin should be replaced if there is damage to the actual pin or if a portion of the pin is missing. Also, the use of multiple pins in a splice is not recommended. It can result in a weakened/shortened splice life, uneven tension on the belt, and unwanted pin migration.
Assessing your splice
During hinge pin insertion or removal you should also take the opportunity to inspect the whole splice, as well as your belt. A quick assessment to make sure the hooks aren’t worn and the belt isn’t damaged could mean the difference between a quick fix and a catastrophic failure.
Authored by: Ramses Banda Marquez, Product Manager
Banda Marquez manages the overall marketing strategy and activities associated with the light-duty mechanical fastener line and belt conveyor products. He brings expertise in marketing, product management, operations, engineering, and supply chain management to Flexco, along with extensive experience in distribution and international business. Banda Marquez also holds patents in both the U.S. and Australia. Banda Marquez earned a bachelor's degree in Mechanical Engineering from Baja California State University and a master's degree in Project Management from Keller Graduate School of Management.