Industry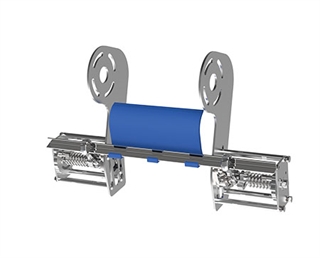
Food Processing – Proteins
Application
Trim Collection Conveyor
Product
FGP-C Food Grade Primary Cleaner for Cleated Modular Belts
Objective
• Product carryback
• Product waste
• Product yield
• Production labor time
• Sanitation time
Conveyor Detail
• 10" wide
• 2" pitch PMB
• 8-tooth sprockets (~6.5" Sprocket + Belt Diameter)
• 1" high x 8.5" wide cleats, centered on belt width on 6" C/C (typ)
• ~28 FPM Belt Speed
Problem:
A leading poultry processor in the south-central United States was facing inefficiencies on its trim collection conveyor, where chicken nuggets and tenders were transported in a wet, high-moisture environment. Excess product was accumulating in catch pans beneath the conveyor, requiring operators to manually transfer approximately 100 pounds of product per day to the next belt. While this wasn’t outright product loss, the additional labor required for recovery significantly increased operating costs. On average, workers spent an hour each day manually moving product. With an estimated overhead cost of $100 per hour, this resulted in $25,000 in unnecessary annual labor costs. Additionally, some product was inevitably lost during this process, further amplifying the financial impact. At $1.50 per pound, product losses could add up to $37,500 per year, which could bring the total cost of inefficiencies to over $62,500 annually. Recognizing the need for a more efficient system, the plant’s operations team sought a solution that would improve material recovery, reduce labor dependency, and streamline production.
Solution:
After consulting with a trusted partner, the operations manager scheduled a site assessment with Flexco to try the FGP-C Food Grade Primary Cleaner for Cleated Modular Belts. Designed specifically for food-grade applications, the FGP-C effectively removes residual product, keeping material within the production flow and preventing costly buildup in catch pans. Available in UHMW and metal-detectable options, the cleaner ensures compliance with food safety regulations while delivering an efficient scraping mechanism that minimizes carryback. After the installation, plant operators quickly noticed a significant improvement—less material was collecting in the catch pans, and product was remaining on the belt where it belonged. The simple installation process required minimal downtime, seamlessly integrating with the existing system. Encouraged by the immediate results, the team considered installing the FGP-C across multiple lines in the facility.
Result:
Following full implementation, the facility documented $25,000 in annual labor savings by significantly reducing the need for manual cleanup and intervention. In addition, based on observed improvements in system efficiency, the team estimates up to $33,750 in potential annual savings from recovered product (a 90% improvement in recovery efficiency). Combined, these gains represent a potential total cost reduction of $58,750 per year. The payback period, based solely on the documented labor savings, was just 22 weeks (155 days). When factoring in both labor and estimated product recovery, the investment paid for itself in as little as 66 days. Beyond the financial impact, the FGP-C improved sanitation processes across the facility, reducing cleanup time and allowing workers to shift their focus to higher-value tasks. The plant also experienced a noticeable drop in water usage, contributing to reduced operating costs and supporting sustainability goals. With increased efficiency, less waste, and greater profitability, the facility strengthened its ability to maintain a safe, compliant, and high-performing belt conveying system.
What Does Flexco Accumulating Value Mean?
When you see the Flexco Accumulating Value (FAV) icon, you can expect a Real-Life Result that represents the measurable, repeatable value added to an operation through its investment in a Flexco solution.
FAV results document the ongoing dollar value realized with implementation of Flexco products or services and details how that value helps operations achieve and maximize their productivity, efficiency, throughput, output, and uptime.